Cost reduction and productivity increase in basket truck fleet
When it comes to the rental of trucks with baskets, there are unsolved challenges that cause unexpected problems and costs for rental companies and that can be solved through the digitalization of the fleet for basket trucks. These can be summarized as follows:
1. Detection of boom truck support.
2. Basket position detection.
3. Detection of the existence of force in the basket.
4. Immediate detection of alternator fault.
5. Capture hours, machine, and automatic check up notification
6. Remote machine parameter request and modification
This information, captured through the digitization of the fleet for basket trucks, and properly processed, can help a rental company of this type of machine to quickly and remotely solve typical breakdowns that would otherwise require a lot of time and resources to resolve. In addition, in most cases, these breakdowns are caused by bad practice on the part of the customer, perhaps due to a lack of knowledge and practice, which could also affect thesafety of the operators.
In this case, and 6 months after the digitalization of our client’s fleet, we have obtained:
1. A 30% reduction in technical actions with field travel (all information is available on the mobile) due to breakdowns caused by poor handling, and, therefore, a proportional reduction in operating costs.
2. An increase in the improvement of customer service by solving many faults remotely and independently of the information provided by the customer by having objective information of the machine in real time. Additionally, the time spent on resolving at least 30% of this type of fault is less than 5 minutes.
3. An increase in the time available for tasks not performed by machines, such as repairing machines.
4. An increase of 20% in the performance of the technicians involved in the resolution of faults in the field, since they work with objective information of the machines, and greater independence of the level of knowledge of the technician involved.
Technical Director of our client: With more than 1300 machines spread throughout the country, the number of breakdowns at the end of the day is of a significant volume. Many of them are due to bad practice or lack of knowledge on the part of the client, so they can be solved remotely, as long as objective information obtained remotely through fleet digitalization is available. The digitalization of B’Smart’s fleet has been a real breakthrough, allowing us to reduce costs and increase productivity and the quality of customer service considerably. In addition, we have been able to benefit from the current digitalisation aid.
Is the digitization of a machinery fleet an expense or an investment…?
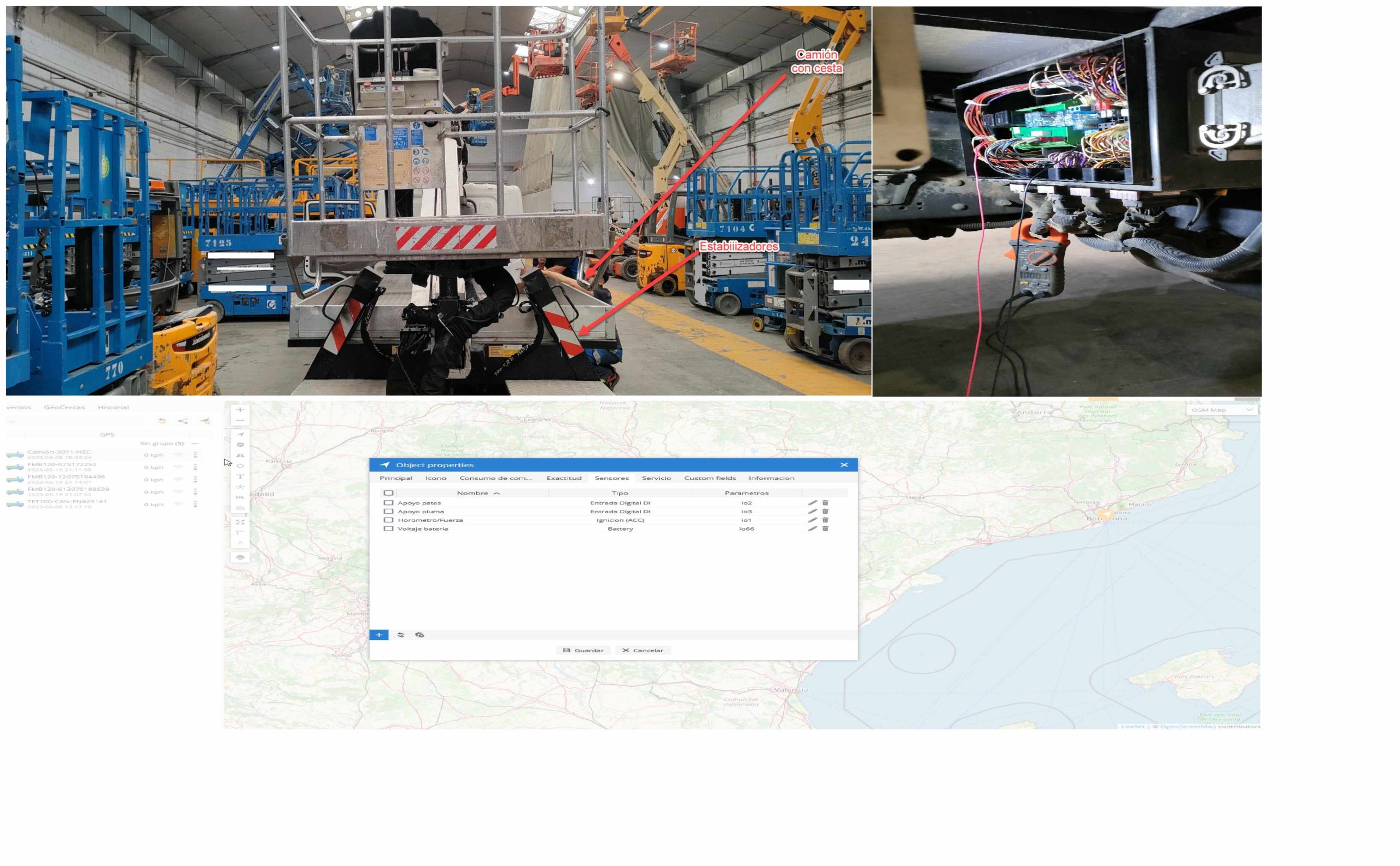
Digitalization of the basket truck fleet