Reduction of the breakdown rate in the electrical machinery fleet
Our client, a machinery rental company operating in Spain, with more than 1000 electrical machines and a high percentage of incidents in the machinery fleet, asked us for a solution to minimize this incident that generated high and unforeseen costs. Some of the incidents focused on:
-
- Lack of water in the electrolyte that shortened the life of the battery.
- Presence of water in the chest that produced corrosion.
- Poorly performed charges on lead-acid batteries that affected battery life.
- Discharge of batteries below the recommended limit in lithium batteries.
- Incidents due to insufficient loads by your client.
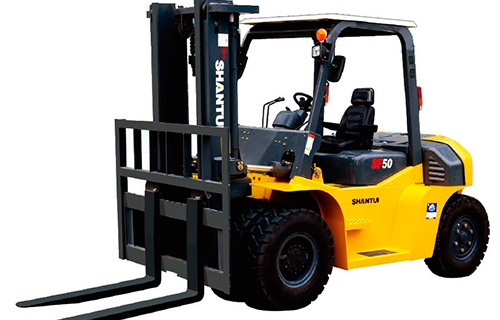
Therefore, our client asked us for a solution to minimize the aforementioned high rate of incidents that generated high and unforeseen costs. To solve the challenge, the digitalization of B’Smart’s fleet has been implemented, being able to know:
-
- Real-time charging and discharging periods and battery voltage.
- Lack of water in the battery elements and presence of water in the chest.
- Battery temperature and Charge and discharge intensity.
- Impacts and aggressive driving.
- Identification of the driver.
- Speed limitation by zones.
- Machine hours, operating periods and automated notification of revisions.
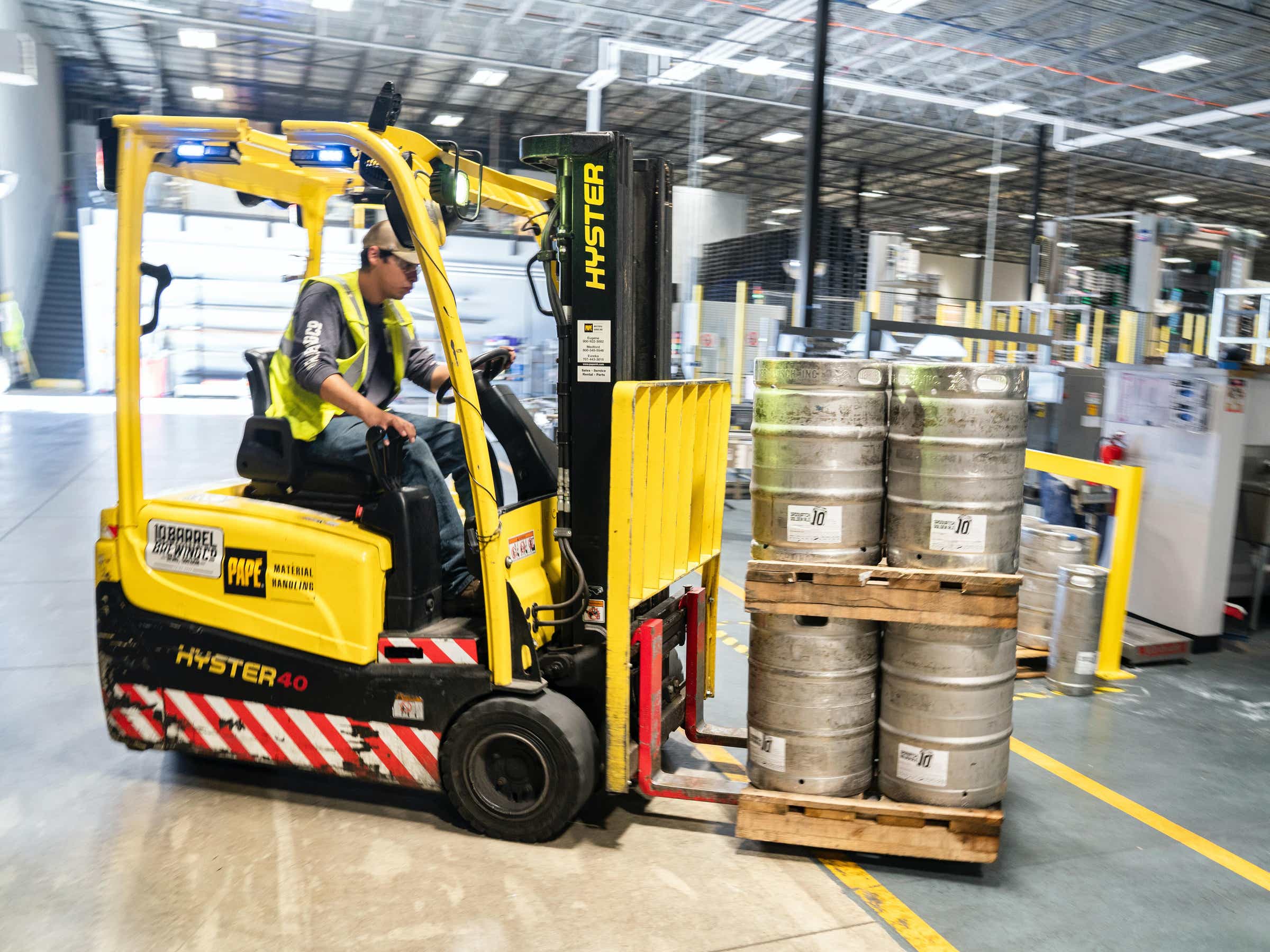
Technical Director of the company;
Since the implementation of B’Smart’s fleet digitalization, we have achieved a significant reduction in breakdowns in our fleet of electrical machinery, among other things:
-
- Reduce by 90% the incidents due to lack of water in the batteries, increasing their useful life.
- Reduce corrosion in the chest due to the presence of water by 90%.
- Totally mitigate aggressive machine driving and associated risks.
- Reduce technical visits to the customer due to lack of battery charge.
- Increase the quality of customer service by reducing the number of incidents and the time to resolve them, since 30% of them are resolved remotely.
- Reduce the hours dedicated to the control of preventive maintenance by 60%.
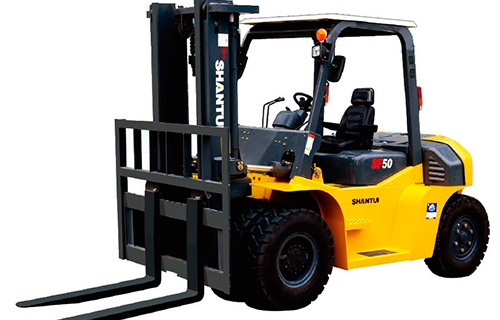
In addition, all the data collected is stored and sent to our ERP, which facilitates the automation of manual and repetitive tasks that do not add value. The benefits we have obtained after fleet digitalization are:
-
- An increase in productivity.
- A reduction in costs by reducing breakdowns and their severity.
- Increased control over the machinery fleet and daily tasks.
- An improvement in operational efficiency by having objective data immediately, such as the detection of the lack of water in the elements of a traction battery.
- An increase in the quality of customer service by reducing the number of breakdowns, the severity of the breakdowns and reaction times.
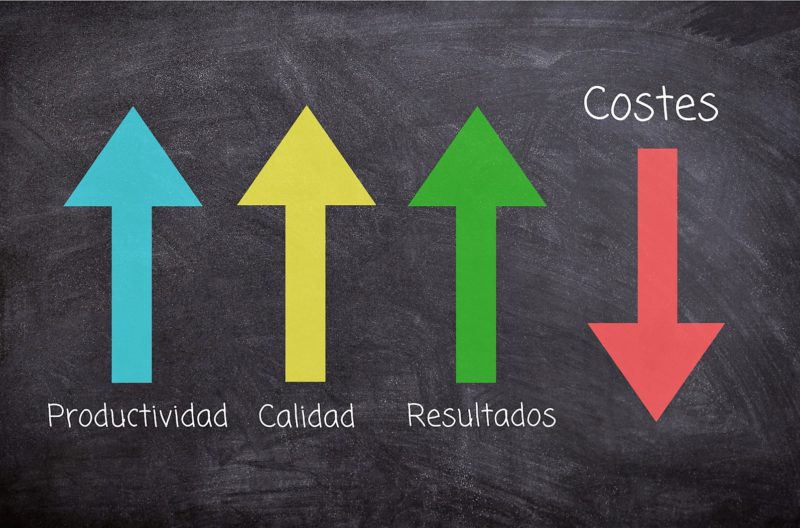
CEO of the company:
We have calculated that the return on investment after the digitalization of the B’Smart fleet is 5 Euros for every Euro invested. In addition, we have eliminated many headaches related to the maintenance of traction batteries.