The customer
Our client is a machinery rental company in the province of Malaga with more than 200 machines including lifting platforms, generators and various machinery. Increasing the life of traction batteries in electric machines and reducing breakdowns has always been a pending challenge.
The challenge; increase of battery life in electric machines
Our client has more than 200 machines of all kinds, among which there are generators of various types, lifting platforms, bulls, etc. Which are rented in different geolocations of the Iberian Peninsula. When a machine suffers a breakdown, a technician of our client must travel to check the machine, with which the technician, sometimes, has to make trips of 400 km and many times on weekends. The problem arises when the technician moves at that distance and the breakdown is given by the lack of battery, a discharge below 20%, or any other fault not detectable remotely due to the lack of a remote measurement of the battery of the machine. Thus, since the machine does not have a system that allows to know the battery level remotely, it is only possible to know it once the breakdown is attended.
The solution; Implementation of Fleet Digitalization to Increase Battery Life of Electric Machines
Using smart fleet management it is possible to know:
- The state of charge and discharge of the battery, since a lead acid battery has a maximum of 1500 charges.
- The existence of water in the elements.
- The Fall of Water in the Chest
- The temperature of the battery.
- Battery discharge level (lithium batteries should not fall below 20%).
Based on this data, alarms can be generated before the battery is completely discharged, the charge/discharge history can be displayed, notified via SMS or mail, etc. Thus, by constantly measuring the battery voltage of the machines, our customer can know the status of the battery at all times. Thus, the fleet management system can automatically notify your customer by mail or SMS before a problem occurs, for example, when it is lowered below 20% load. In this way and through the remote measurement of the battery voltage, breakdowns and unnecessary displacements are avoided and customer service is improved.
Then we see the graph that indicates the historical voltage in the battery
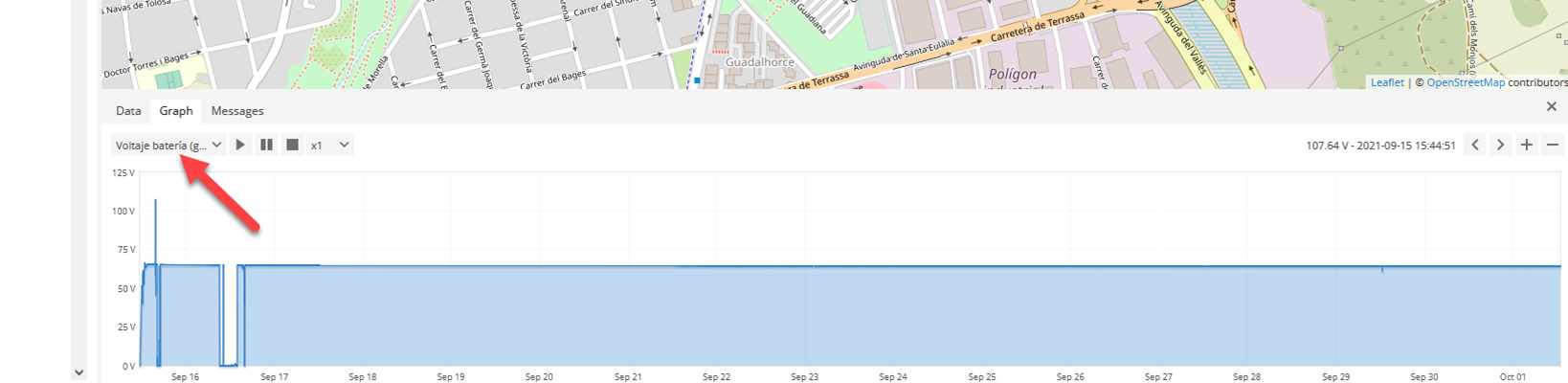
The following graph indicates the existence of water in the elements
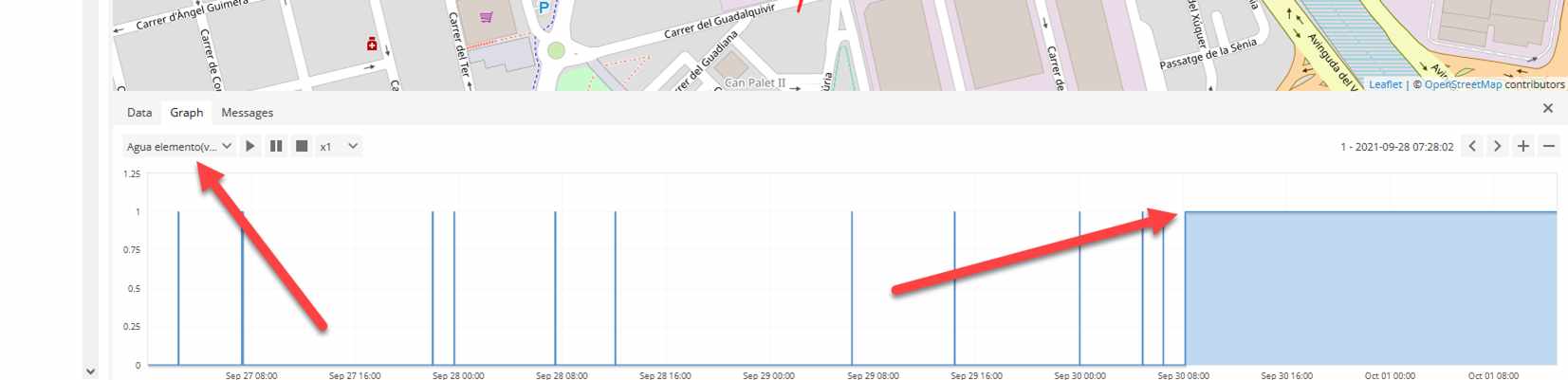
The customer
Thanks to the fleet management of B’Smart and the remote measurement of the battery voltage of the electric machines we have improved the customer service reducing response times, the number of incidents, while extending the life of the batteries.