There are systems on the market that can provide us with information about the water level in the electrolyte and the water temperature in the elements of a traction battery. The only problem is that such systems, unlike fleet management for electrical machinery, offer the information only at the local level, and the interested party, (machinery rental company), does not receive such information, which could help him to:
- Increase productivity
- Reduce costs
- Increase customer loyalty
Implementing fleet management in a fleet of electrical machinery is therefore a paradigm shift. Fleet management for electrical machinery changes the way of working on the basis of objective data and not based on assumptions that are difficult to demonstrate when, for example, a customer calls the machinery rental company with a problem with a machine he has rented. On the other hand, it is true that there are systems that indicate the level of water in the element of a traction battery, and even the temperature of it. However, the problem with these systems is that the information they offer is only local, and, therefore, the fleet manager, who is the one who assumes the costs, cannot make use of that information to solve problems and improve.
Below we describe some of the advantages and improvements that we will achieve with the implementation of fleet management for electrical machinery:
- Geolocation of the machine outdoors and indoors; in addition to providing information on where the machine is, it can provide information on the performance of the personnel, or for example information on aggressive driving, speed limitation, etc.
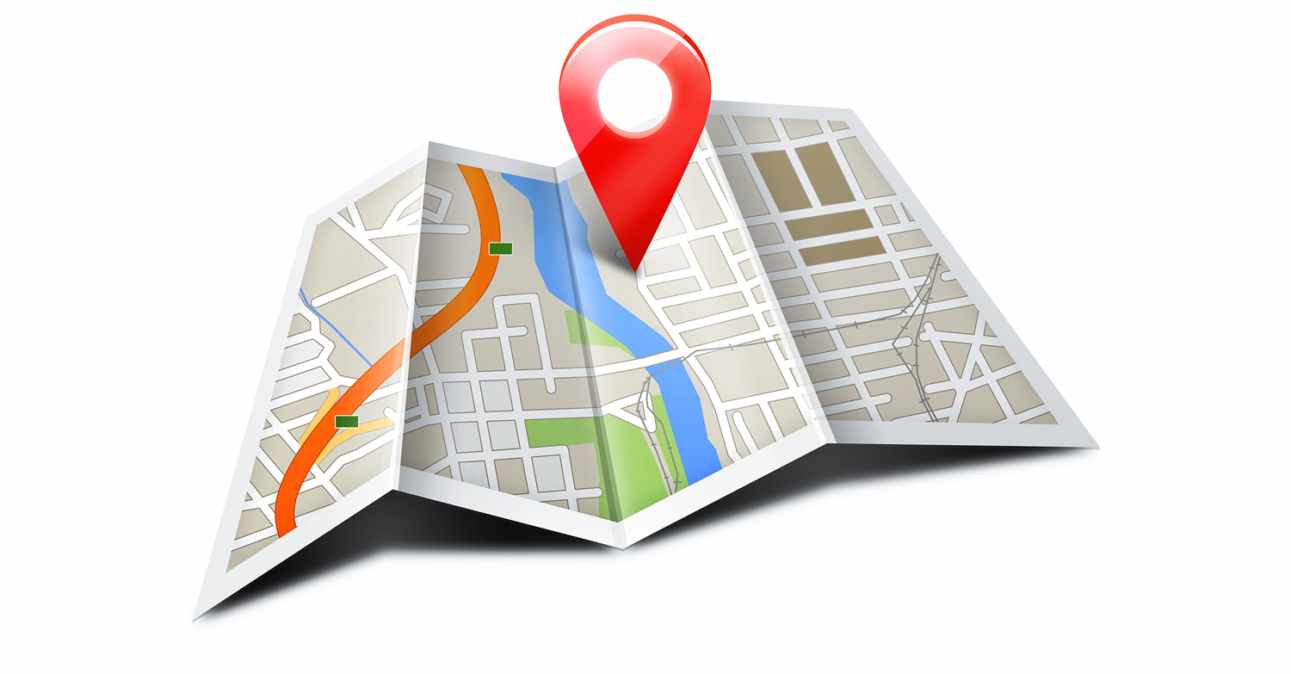
- Remote capture of machine hours; It will help us to reduce manual and repetitive tasks such as collecting and entering hours in the management software or Excel manually. Since the fleet management system for machinery performs the capture of hours and the management of revisions automatically.
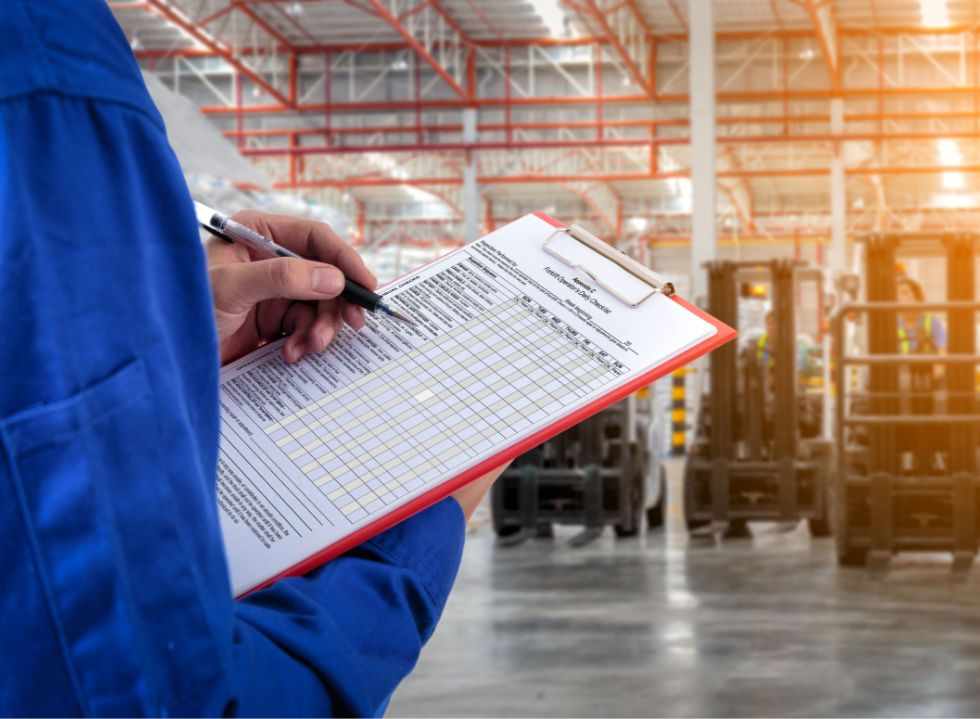
- Charge cycle monitoring; Provides information on when the machine is connected and disconnected and the battery charge level, and can generate alarms and reports that show the charge and discharge of the battery.
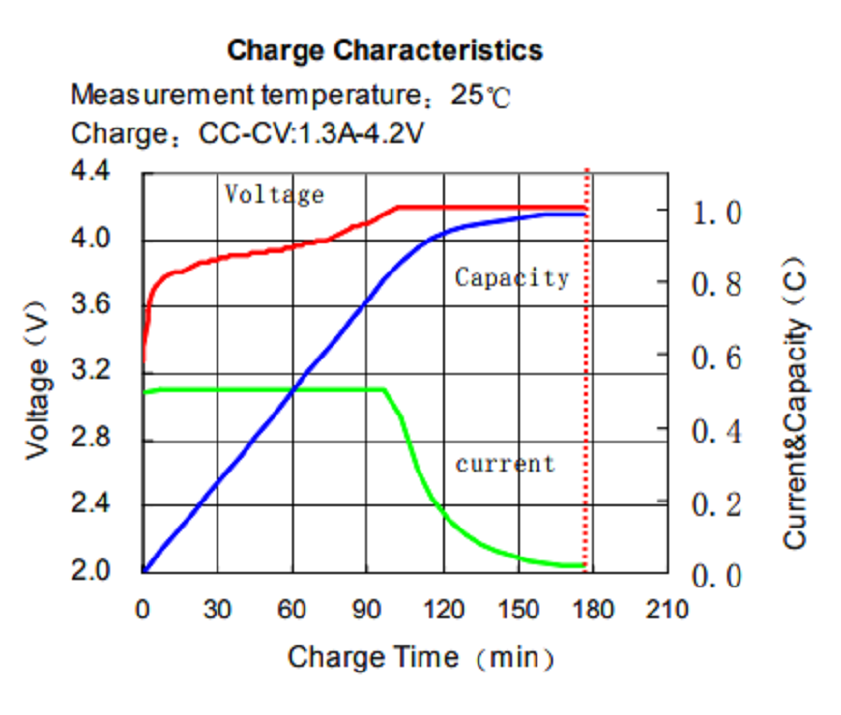
- Remote monitoring of the battery voltage; It will provide us with information on the status of the elements, or at what point of discharge the battery is at. Being the critical charging point of a 20% traction battery, as indicated in the following article, it is advisable that it is not used below this value. In this sense, the fleet management system for electrical machinery, will launch the corresponding alarm when this end occurs.
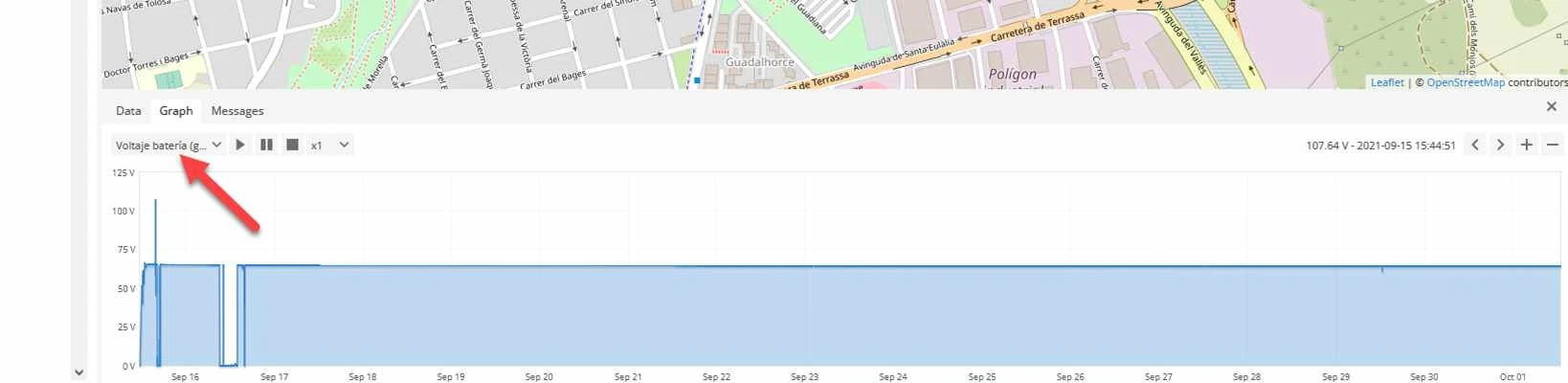
- Monitoring of the water level in the cells; When there is a lack of water in the cells, the battery heats up above the temperature recommended by the manufacturer and its useful life is reduced, as well as increasing the probability of battery failure. Fleet management for electrical machinery will launch a previously configured alarm, provided that this temperature is above the configured temperature.
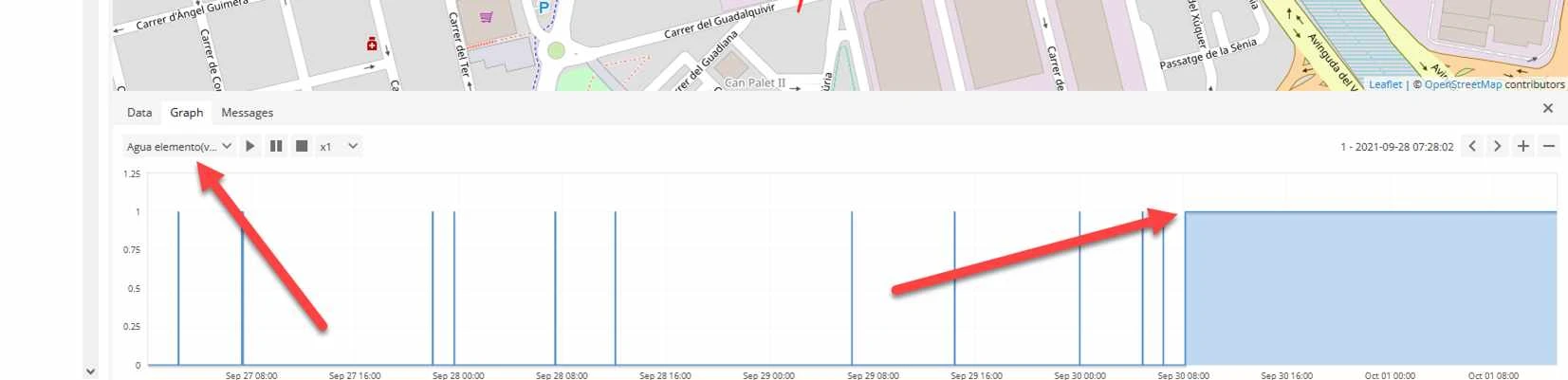
- Detection of water in the casing; It is a recurring problem that when water is added to the elements, it falls into the casing and causes corrosion. The fleet management system will launch an alarm every time water is detected in the chest of a battery in the fleet.
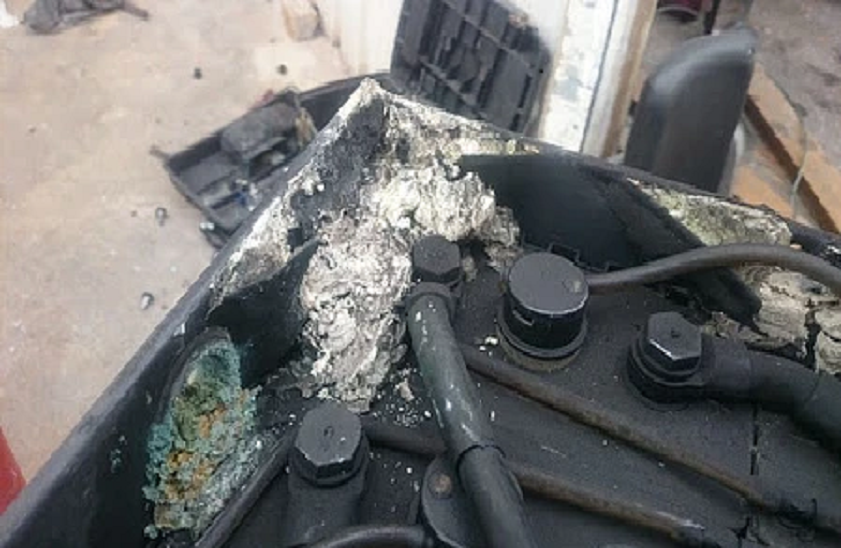
- Battery temperature monitoring; Malfunctioning charger or lack of water in the elements can cause the battery temperature to rise above the manufacturer’s recommendation. This is something that fleet management for electrical machinery will also help us to monitor and control with quickly installed Bluetooth temperature sensors.
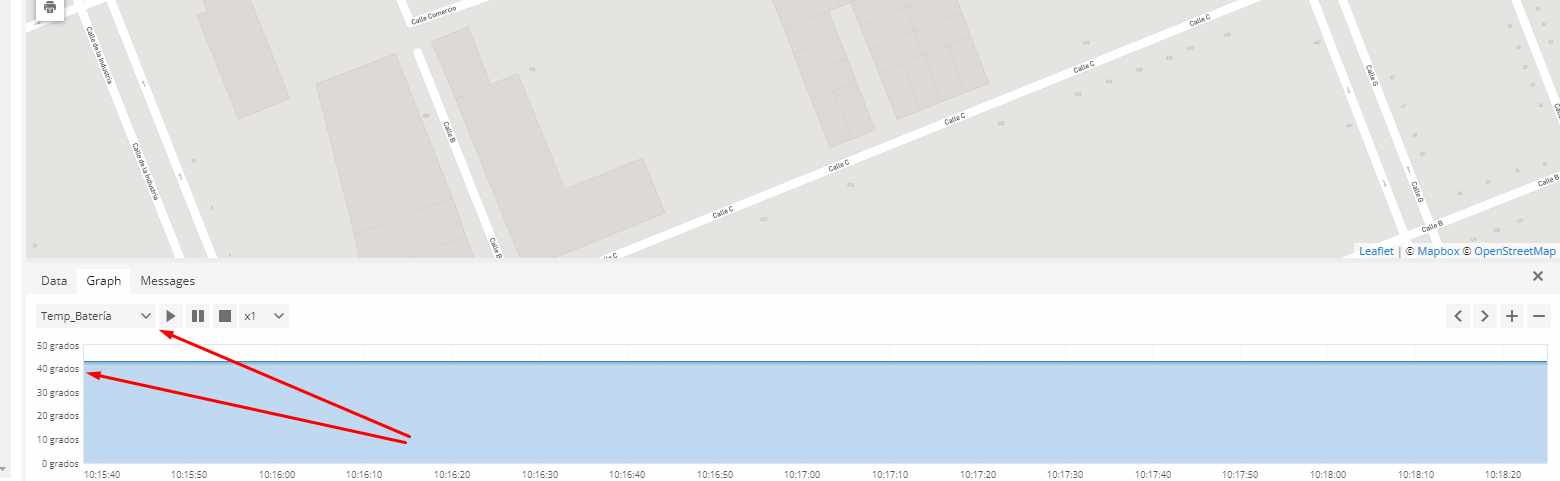
Thus, it is more than justified to implement fleet management in electric machinery, which also pays for itself within a few months. If you want to see a use case for this type of machine, do not hesitate to consult this article.